1 Introduction
New occupational exposure limit values apply to the whole industry. Already for electrical installation work on construction sites during the milling of slots, the new limit values mean an adaptation of the previous construction sequence. In other industrial sectors, the effort is much more extensive, as these are linked to many peripheral conditions. In tunnel construction, e. g., access to the workplace is restricted and project planners and health protection coordinators are faced with major tasks.
In mining, however, the most difficult conditions arise. Many workplaces with a wide variety of requirements are located in underground operations with severely restricted access to supplies.
For over a year now, many companies and mining groups have been working together with machine manufacturers, health protection specialists and government agencies on future-oriented solutions to implement the new workplace limits in mining and at the same time be competitive on the international market.
But what are the current rules and how must ventilation be changed?
2 Rules/Limit values
Health protection in mining is regulated by the Health Protection – Mining Ordinance (Gesundheitsschutz-Bergverordnung –
GesBergV) with the Hazardous Substances Ordinance. However, this does not itself contain any direct occupational exposure limits, but refers to the Technical Rules for Hazardous Substances (Technische Regeln für Gefahrstoffe – TRGS).
The decisive factors for ventilation and air quality are individual factors:
- TRGS 400: Risk assessment for activities with hazardous substances;
- TRGS 402: Determination and assessment of hazards during activities with hazardous substances: Inhalative exposure;
- TRGS 554: Exhaust gases from diesel engines (new since January 2019);
- TRGS 559: Mineral dust;
- TRGS 900: Occupational exposure limit values;
- TRGS 906: List of carcinogenic activities or processes according to §3 Abs. 2 Nr. 3 GefStoffV.
If the rules specified in the TRGS are complied with the actual technic, it can be assumed that the requirements are met and no further measures are required.
In particular, nitrogen oxides (mainly after blasting), diesel emissions (transport vehicles, mining machinery, etc.) and dust pose a major challenge for mining. Dust containing quartz is classified as carcinogenic.
Since May 2016 with entry into force on 4th November 2016, the TRGS 900 has set the workplace limit values for nitrogen monoxide (NO) at 2ml/m3 (ppm) and nitrogen dioxide (NO2) at 0.5 ml/m3 (ppm). Diesel engine emissions were reduced to 50 mg/m3 = 0.05 g/m3 in May 2017. These values are currently valid and must be adhered to in industry.
In addition, the new TRGS 554 came into force in January 2019. Here the definition of “exhaust gases from diesel engines” is further concretized. Essentially, exhaust gases from diesel engines contain diesel soot particles, NO, NO2, carbon monoxide (CO) and carbon dioxide (CO2). The term “diesel soot particles” corresponds to the term “diesel engine emissions” in the sense of TRGS 900. Also in TRGS 554 the AGW for diesel soot particles according to TRGS 900 in the amount of 50 µg/m3 (A) and the AGW mentioned above for NO and NO2 are now mentioned. It is stated that no acute or chronic effects on the health of employees are to be expected if the AGW is complied with and that therefore no carcinogenic activity according to TRGS 906 is present.
Since 2016, a five-year transitional period until 2021 has applied to mining operations. At the end of 2019, the measures implemented to date by mining operations will be reviewed.
CO emissions are also expected to be reduced from currently 30 to 20 ppm.
What difficulties or influences are the limit values associated with in the ventilation of the mines?
3 Influences on the ventilation of a mine operation
If the mining operation’s extraction capacity is not to be reduced by using the current equipment underground, an increase in the volume of fresh air by a factor of eight to ten would be necessary in most operations. This cannot be achieved for various reasons. An economical solution lies in the optimization of all individual components which have a direct or indirect influence on the ventilation. When considering the three main emitters of explosive gases, diesel exhaust gases and dusts, the main problems of limit value reduction become clear.
Since only the influence on ventilation is brought into connection here, the aspect of an operational restriction of the use of explosives and diesel vehicles is not pursued further.
3.1 Explosive Gases
While on most tunnel construction sites explosive gases can be released relatively quickly into the open air, in underground mines the extensive network of tunnels and chambers is more problematic. The nitrogen oxides (NOx)spread increasingly and remain in the pit for a long time due to relatively low weather speeds. The working areas in the rear area are directly affected. K + S AG has already successfully developed a new explosive to reduce NOx during blasting. Any remaining NOx must now be carefully guided out into the open. The ideal solution for this would be a free cross-section that is not integrated into working operation. For many companies, however, this means a massive change in the complete weather conditions. A local bridging of the work places located in the exhaust air direction by means of additional air ducting seems possible at first glance in individual cases. However, the actual concentrated collection of the explosive gases must be realized as well as leakage-free ducting as far as possible, as otherwise a minimum concentration due to overpressure in the duct runs in a circle and remains in the tunnel. The new limit values should not be underestimated at such points. For this reason, this variant should be carefully considered and implemented only as an emergency solution.
3.2 Diesel emissions
As a result of the progressive mechanization of mines, more and more diesel-powered vehicles are being used for transport, loading, mining or as semi-mobile equipment underground. In order to comply with the new DME limit values with the same existing fresh air, about six to seven out of ten vehicles would have to be decommissioned. According to TRGS 554, each vehicle must be supplied with a minimum quantity of fresh air to be delivered into the working area – in mining 3.4 m3/min/DkW. In order to remain with diesel-powered vehicles, the manufacturers of the engines are of course first and foremost called upon to reduce emissions. Realistically speaking, it is not possible to reduce emissions to 1/10. But each approach in the sub-areas leads to a possible superordinate multiple solution. The new TRGS 554 of January 2019 has also been extended to include the definition of the “DeNOx system”. These are exhaust aftertreatment systems to reduce emissions of NOx.
A conversion to electric vehicles can become a mammoth project for the mine from various aspects. Charging stations, e. g., have to be set up that place higher demands on the electrical supply to the mine and work processes have to be logistically adapted to the power and mileage of the electric vehicles. Electric vehicles for demanding operations are not yet fully available for all areas.
In terms of ventilation, completely different questions arise: How can an electric vehicle that has caught fire be safely extinguished? What flue gases do they produce? These questions remain unanswered at this stage.
Irrespective of various partial solutions, the operation of vehicles must be optimised by means of ventilation management. Each company must evaluate the depth at which this is carried out and the aids used to do so, for itself and for the specific requirements.
Real-time sensors for measuring local pollutant concentrations are an aid for partially or completely intelligent weather control. Depending on the existing digitalized weather network, these can be integrated and contribute efficiently to the optimization of the available weather for vehicle use.
3.3 Dust
The measurement of dust takes place over a certain period of time and is evaluated retrospectively. A recognized real-time measurement is currently not available and can therefore not be integrated into a sensor system for flexible ventilation optimization. Dust should be avoided as far as possible or collected and filtered directly at the point of origin. Otherwise, it is difficult to comply with the limit values. Fixed installations, such as belt transfers or drilling rigs, are technically easy to remove dust from. It becomes more difficult with roadheaders/continuous miners (CM) or dusts from driving distances. Enclosure is only partially possible or difficult to implement. Especially with the CM, a certain peripheral dust development is almost unavoidable during the first cutting. The machine operator is in the endangered area due to the proximity to the cutting head. This is not a new problem, but with new limits it is all the more acute.
4 Ventilation problems
Undoubtedly, an increase in the amount of weather for the entire pit by about ten times is not feasible. Mining companies must pursue a multiple solution strategy in order not to change the entire ventilation and operating concept. However, it will be necessary to locally increase main weather and special ventilation volumes.
4.1 Main weather
High main weather volumes imply high air velocities and higher operating pressures. The loads on the existing pit lining are increasing extraordinarily. Weather structures and shaft installations are subjected to higher loads and must be reinforced or renewed. The higher pressure at these structures also causes a higher leakage, so that seals need to be repaired. In some cases, it is no longer possible to work with higher speeds in the lines (permissible maximum speed for the weather in working areas < 6.0 m/s). Fine dusts rise and are transported through the mine. The air density can change slightly, which sooner or later leads to a saturation of the emissions in the supplied weathers.
4.2 Special ventilation
In the area of special ventilation, higher volumes with the same space conditions generate higher pressures with the same duct size. The influence of the pressure increase on the duct diameter is approximately x5. The exemplary considerations of pressure conditions in Figures 1 and 2 provide an overview of the conditions in ducts.
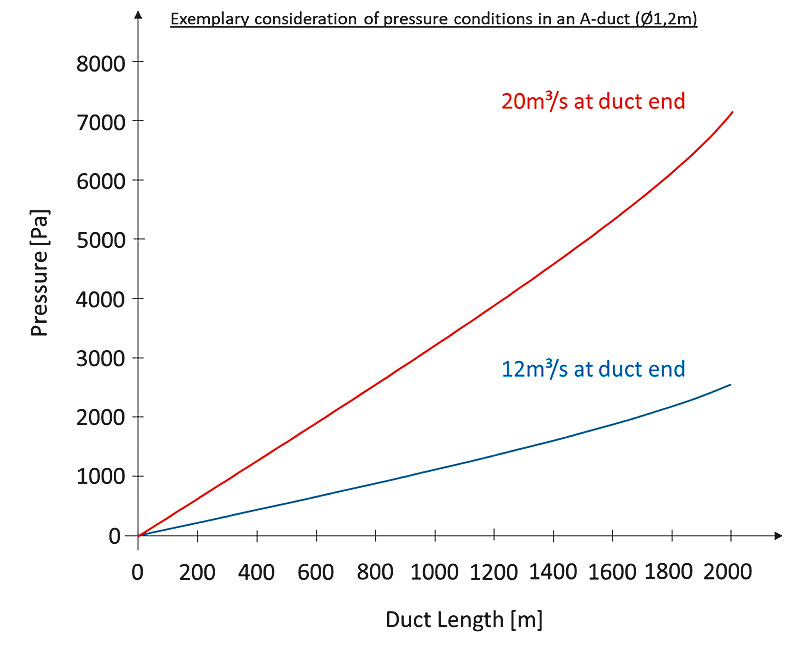
Fig. 1. Exemplary consideration of the pressure conditions as a function of the duct length. // Bild 1. Beispielhafte Betrachtung der Druckverhältnisse in Abhängigkeit von der Luttenlänge.

Fig. 2. Exemplary consideration of the pressure conditions as a function of the volume at the duct end. // Bild 2. Beispielhafte Betrachtung der Druckverhältnisse in Abhängigkeit vom Volumen am Luttenende.
In addition, the additional pressure increases the requirements both on the quality of the duct and on the maintenance or repair. Another consideration is the additional heating of the weather. For every 1,000 Pa increase in pressure at the fan, the air becomes about 1 K warmer. Climate control must therefore also be included in the consideration of a solution.
In general, a considerably higher energy input is required for main and additional ventilation. Physically, a linear increase in volume increases the pressure quadratically and the required motor power cubically. For this purpose, energy networks, fuses, cables and cable routes must be redesigned many times. Efficient control and regulation systems for all components are capable of optimally adapting the corresponding outputs at any time. This leads to efficient utilization of the components and avoids overdimensioning, which would demand a multiple of the infrastructure.
Particularly in ventilation, the individual components can be optimized in the overall concept through intelligent networking with sensors. “Ventilation on Demand” with higher-level process control and ventilation program including simulation options can work efficiently and flexibly thanks to integrated sensor technology. Logistical processes can thus be coordinated and planned with regard to ventilation technology. Even a single air duct drive can be controlled independently, intelligently and fully automatically according to today’s state of the art. Not only weather requirements are precisely controlled, but also the air duct condition can be monitored by integrated process analyses. In this way, weather requirements can be correctly assigned and exploited in order to avoid bad weather and energy losses.
5 Conclusion
As long as humans are not completely released from the work process, the ventilation of the mine must be adapted to the new limits in the future. This can be done efficiently after the analysis of the real possible reductions of the different emissions. In order to keep this weather optimization energetically small, a superordinate process control including measured value capture in the critical work areas is recommended.