1 Introduction
divider]
In Poland and formerly in Germany suspended monorail locomotives (SML) are the backbone for underground transport of personnel and materials in underground hard coal mines. Driving along a suspended monorail track below the roof they operate independently from the floor conditions. On the market, there is a wide variety of diesel-driven or battery-powered SMLs available for underground coal mining applications (1). Diesel-driven SMLs generate emissions like hazardous gases, heat and noise and puts the necessity to transport fuel to underground workings (1). Battery-driven machines lose operational time during recharging, which has to meet high requirements if applied in the potentially explosive atmospheres of underground coal mines (2). These disadvantages create a need for alternative drive concepts resolving around electrification of transport.
This paper introduces two separate European-funded projects. The project “Increase of mines efficiency and health protection through the innovative transport system based on BUSDUCT” (BUSDUCT) and the project “Innovative high efficiency power system for machines and devices, increasing the level of work safety in underground mining excavations” (HEET II). They will both present innovative concepts for the electrification of underground transportation in coal mines using SMLs. Consequently, leading to increased health protection by avoiding emissions from diesel-driven machines and to improve the productivity of the transport system. Both projects aim to design and develop prototypes for underground coal mining environment. By doing so they consider the applied explosion protection standards in the EU.
The publication will start with an overview on fundamentals of methane gas, explosions and explosion protection measures. It will continue with presenting the BUSDUCT project concept, followed by the HEET II concept. The paper concludes by illustrating on the challenges both projects face on their way from concept to implementation.
2 Fundamentals
2.1 Methane in underground coal mining
Methane is a colourless and odourless gas (3). It is the simplest member of the paraffin series of hydrocarbons (4). Under standard conditions, methane has a density of 0.656 kg/m3. Table 1 shows selected properties of methane.

Table 1. Flammability properties of methane (5, 6). // Tabelle 1. Sicherheitstechnische Eigenschaften von Methan (5, 6).
The ambient pressure and temperature influence the LEL and UEL of methane. An increase in temperature and pressure increases the flammability range of methane. The influence of pressure and temperature is negligible for LEL, while there is a significant influence on the UEL (7).
Methane is produced as a by-product of the coalification process. Part of the methane that is entrapped in the coal is released continuously and the rate of release depends on a variety of parameters including methane content, the permeability of the cleat system, the degree of fracturing of the coal and the extent of the mining activity. Methane normally enters the active mine workings as a localized source at elevated concentrations and is then mixed with the mine air and consequently diluted. In case of insufficient ventilation volume flow rates methane tends to form layers. (7)
2.2 Explosion protection
An explosion is an abrupt oxidation or decomposition reaction which produces an increase in temperature and pressure (8). For an explosion to occur under atmospheric conditions, flammable material, oxy-gen and a source of ignition need to be present at the same time. If air and flammable gases, vapours, fog or dust that can be ignited under atmospheric conditions mix, an explosive atmosphere is created.
To prevent explosions from occurring, explosion protection measures need to be applied. Explosion protection measures are divided into the following three categories:
- Primary explosion protection measures, which are all technical measures that prevent or restrict the occurrence of an explosive atmosphere.
- Secondary explosion protection measures, which are all technical measures that prevent the occurrence of an ignition source.
- Constructional explosion protection measures, which are all technical measures that reduce the impact of an explosion to an acceptable level. (9)
2.3 Legislation overview
For the development of prototypes for the application in an underground coal mine environment, it was required to consider the relevant standards in the geographic region. In the EU, the European Commission Directive 2014/34/EU (ATEX) sets the requirements for the operation and manufacturing of equipment to be used in potentially explosive atmospheres (10). In China, the Guobiao system is applied together with standard GB3836. In the USA, the legislation of Hazardous Locations aims at controlling the risks associated with explosions. In Australia, the New South Wales Coal Mine Health and Safety Regulation and in Brazil the INMETRO Regulation Portaria 83:2006 state the requirements for electrical equipment used in explosive atmospheres. Special focus for the projects presented in this paper is the ATEX directive. (11)
3 BUSDUCT
3.1 Project overview
The project “Increase of mines efficiency and health protection through the innovative transport system based on BUSDUCT” (BUSDUCT) was funded by the Research Fund for Coal and Steel (RFCS) of the EU. It was conducted from 2019 to 2022. The project consortium consisted of the following members:
- Instytut Techniki Gorniczej KOMAG (KOMAG), Poland;
- Becker-Warkop SPZOO (BECKER-WARKOP), Poland;
- Polska Grupa Gornicza SA (PGG SP. ZOO), Poland;
- RWTH Aachen University (RWTH), Germany;
- Bartec Varnost (BARTEC VARNOST), Slovenia.
The consortium consisted of the research institutions KOMAG (project leader) and the Institute for Advanced Mining Technologies (AMT) of RWTH, Becker as a manufacturer of SMLs, PGG as a coal mine operator in Poland and BARTEC VARNOST as a manufacturer of electrical equipment for underground mining applications.
The international project consortium aimed to develop a prototype of a suspended monorail locomotive (SML), which is powered with electrical energy via a busduct. The application area of the developed prototype is underground hard coal mining. Thus, the design was conceptualised as explosion-proof. The prototype was conceptualised to be operated without diesel emissions, achieving a travel speed of up to 4 m/s with approximately 30 % less weight than comparable battery-powered monorail locomotives.
3.2 Concept
The prototype of the SML to be developed was designed to drive forward and backwards on the monorail with up to 4 m/s powered by a three-phase (500 V AC) busduct. A busduct consists of a duct made out of metal or resin that contains metallic strips or bard made out of copper aluminium. Busduct presents an alternative to conducting power via cables. The busduct to be used in this project consisted of four single lines. Contrary to previous projects attempting to power suspended monorail locomotives electrically with busducts an open type of busduct is used (12). Two current collectors (CC) draw power from the busduct lines. Each CC consists of four single brush collectors. Figure 1 presents an extract from the prototype model focusing on the busduct and a single CC developed by KOMAG.

Fig. 1. SML concept of the BUSDUCT project (left), location of the busduct in relation to the suspended monorail (bottom), busduct and CC in detailed view (right). // Bild 1. EHB-Konzept des Projekts BUSDUCT (l.), Lage der Stromschiene (unten), Stromschiene und Stromabnehmer in der Detailansicht (r.). Source/Quelle: KOMAG
To use the prototype SML in potentially explosive atmospheres, the CC has to be isolated from the mine atmosphere as ignition source due to electrical sparks cannot be entirely prevented. For this purpose, inert gas is supplied to the inside of every single brush collector in which the ignition source resides. The inert gas in use for the project BUSDUCT is nitrogen. A nitrogen generator will be an integral part of the prototype SML. This nitrogen generator will filter nitrogen from the surrounding mine air and supply a stream of nitrogen with at least 95 vol.-% purity to every single brush collector of the two CCs. Every single brush collector is supplied with nitrogen via two pipes. Given the two CCs on the SML, each of which consists of four single brush collectors, a total of 16 supply pipes will be installed.
To properly isolate the single brush collector from the mine atmosphere sealings are necessary that also help to contain the nitrogen-rich atmosphere inside the single brush collector. KOMAG designed such a seal as well as the integration of the nitrogen supply channel. In this case, the busduct is considered as an enclosure located in a mining hazardous area, containing potential ignition sources and energized bare conductors. The standardized explosion protection mode applied as a technical rule is the pressurized enclosure, which is defined in EN-IEC 60079-2. The design of such a brush collector and a scale indicating its dimensions are shown in Figure 2. The supply stream from the nitrogen generator is injected into the area around the CC via nozzles.
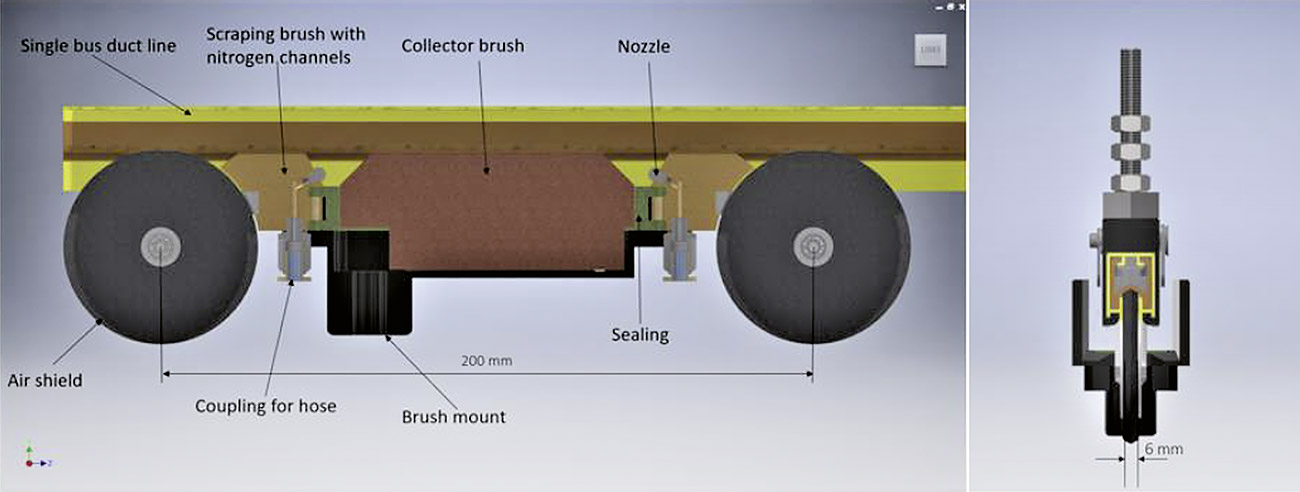
Fig. 2. Cut through single brush collector parallel to driving direction (left), depiction of singe brush collector in driving direction (right). // Bild 2. Schnitt durch Einzelelement des Stromabnehmers (l.), Darstellung des Einzelelements des Stromabnehmers in Fahrtrichtung (r.). Source/Quelle: KOMAG
Based on the developed concept for the safe operation of the busduct and the environmental conditions given in underground coal mines operated by PGG a monitoring sensor system was developed by KOMAG and AMT. Its description will be separated into two distinct sub-systems. One sub-system will focus on the monitoring system for the surrounding mine atmosphere of the SML. As it is an electrical equipment, the SML needs to shut down if the limit value for the methane concentration in the surrounding atmosphere is reached. In underground mine drifts with electric traction, the limit value is 0.5 vol.-% of methane (Polish mining law). The chosen methane was the HASO MPS-1i from the company HASO S. C.
The other sub-system focuses on the inertisation system in proximity to the current collector. A conceptual sketch of the system is given in Figure 3.

Fig. 3. Inertisation system for current collector. // Bild 3. Inertisierungssystem für die Stromabnehmer. Source/Quelle: KOMAG
From the nitrogen generator, a gas mixture with over 95 vol.-% of nitrogen is supplied through a solenoid valve (4), which can open and close. After the solenoid valve, the flow is branched into two main branches in each the pressure is reduced to 1 bar and the flow is monitored via an orifice flow meter (6) PR-28 Smart flowmeter of Aplisens S. A. After the volumetric flow rate measurement, the flow is branched again to supply all single brush collectors of the two current collectors. The brush is sealed to form an undefined and moving pressurized enclosure. As the pressurised enclosure created inside the single brush collector has no defined outlet, monitoring the flow rate at the outlet is not applied. EN-IEC 60079-2 states that a required overpressure of 50 Pa has to be maintained during normal operation and in the period between the occurrence of the explosive atmosphere and switching off the equipment. This minimum overpressure needs to be monitored by pressure sensors (8). The selected pressure sensor for the design phase was the APRE-2000G/Exia/-250…250Pa/0…250Pa/GP in the measurement range of 0 to 250 Pa from the company Aplisens S. A. To monitor the pressure inside the single brush collector, pressure measurement holes were integrated inside the collector brush. An additional pressure sensor was implemented. The Aplisens PC-28/Ex/0-3bar/PK/M pressure converter (9) is installed on the discharge manifold of the nitrogen tank behind the pressure-reducing valves (5). It controls the nitrogen pressure in the supply lines. All listed components are ATEX-certified for underground coal mining applications
4 HEET II
4.1 Project overview
The project “Innovative high efficiency power system for machines and devices, increasing the level of work safety in underground mining excavations” (HEET II) is funded by the Research Fund for Coal and Steel (RFCS) of the EU. The project started in 2020 and will end in 2023. The project consortium consist of the following members:
- Instytut Techniki Gorniczej KOMAG (KOMAG), Poland;
- Politechnika Slaska (SUT), Poland;
- Glowny Instytut Gornictwa (GIG), Poland;
- RWTH Aachen University (RWTH), Germany;
- SWE Spolka z Ograniczona Odpowiedzialnoscia (SWE), Poland;
- Universitatea Dunarea de jos din Galatoi (UDJG), Romania;
- JSW Innowaczje Spolka Akcyjna (JSWI), Poland.
The consortium consists of the research institutions and companies KOMAG (project leader), GIG, UDJG, SUT, and AMT of RWTH, SWE as a manufacturer of composite components and JSWI for supporting innovation processes. The international consortium of the HEET II project according to the SML aims to develop a prototype of a simplified battery-powered suspended monorail locomotive (SML), specifically the tractor system, which can be recharged during driving.
The electric power supply alongside the suspended monorail will be implemented via a single-wire transmission line. Therefore, the second electrical conductor can be omitted, reducing the risk of explosions and electrocutions. The rail, which is commonly manufactured from steel, will be replaced using a newly developed composite rail, making it lighter and less prone to bending. The rail can then be used as the transmitter for wireless power transfer via capacitive coupling to the monorail vehicle. (2)
Additionally, an environmental monitoring system will be placed alongside the suspended monorail. The AMT is developing various modules that will monitor the tractor, the gas concentration of various gases and environmental parameters such as humidity and temperature. These data will be transmitted to surface headquarters for further processing and decision making. (2)
4.2 Concept
First, the focus of the conceptual description will be set on the wireless energy transfer system (WET) developed by KOMAG. It will be followed by a closer description of the monitoring system developed by AMT. An overall overview of the project’s implementations is shown in Figure 4.
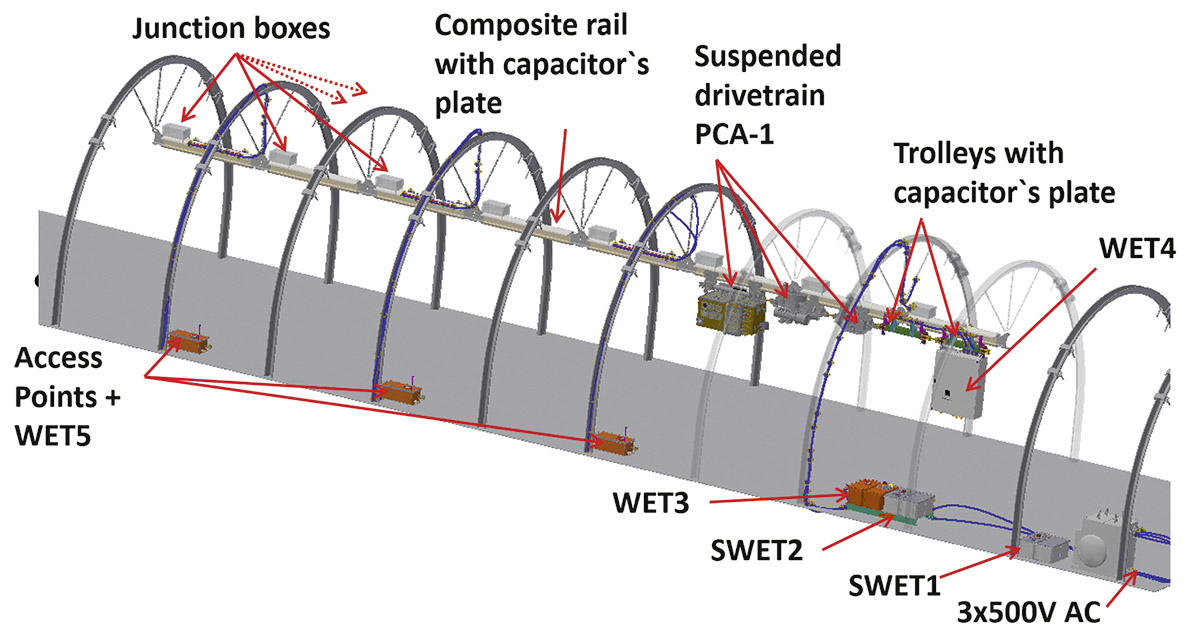
Fig. 4. Visualization of the main modules associated with the SWET and WET system (2). // Bild 4. Visualisierung der wichtigsten Module des SWET- und WET-Systems (2).
To increase the battery runtime of an SML and to prevent special procedures for recharging the battery the HEET II project develops a WET. The coupling elements are capacitor plates installed into a suspended monorail made out of composite material. The second pair of plates will move with the tractor, forming the capacitive coupling. A WET system transmitter (WET3) generates a high voltage, high-frequency current which is transmitted to the receiver (WET4) via the monorail track. The receiver powers an additional charger, which further charges the SML’s battery. The transmitter of the WET system is supplied via direct current. The current is supplied through a single-wire energy transfer (SWET) system. In this single-wire system, the electrical current is closed using a return conductor. The SWET system receives its power by the mine power supply. (2)
The system also features a subsystem related to communication and environmental monitoring. The communication subsystem uses wireless transmission between the suspended tractor, the WETs, and the sensor and communication modules (access points – AP) associated with the suspended route. To eliminate the need to run power cables to these sensor and access point modules, they were also equipped with the WET wireless power system (WET5). The modules feature onboard battery systems to account for down times. (2)
One module of the monitoring system monitors the suspended tractor and the WET4. The information from this tractor module is transferred to AP. The tractor module is connected to the internal tractor system via a controller area network (CAN) bus. Via this connection, it receives status information like the status of the control relays and measurement values like the battery current. These data are aggregated and transferred via Wireless-Fidelity (Wi-Fi) to the closest AP. Various APs are located along the suspended monorail track. They create a Wi-Fi mesh network. The tractor module automatically routes to the closest AP and transfers the above-mentioned data from the tractor. Additionally, the APs are equipped with sensors to monitor environmental parameters. These sensors are gas concentration sensors for the gases carbon monoxide, methane and oxygen as well as the ambient relative humidity and air temperature. The sensor data in combination with the data from the tractor are sent wirelessly from one AP to another up to the gateway module. The gateway module acts as the main connection to the database server, which is located on the surface. The gateway is connected to the server via a single-mode optical fibre, which is used to transfer the aggregated data and information to the database server. (2)
These different modules are all installed in a flameproof enclosure. Components of the system that are on the outside of the enclosure like the sensors for perceiving environmental parameters and the Wi-Fi antenna as well as the power supplies are all ATEX-certified for underground coal mining applications. (2)
5 Conclusion
This paper presented an overview of two concepts for alternative electric supplies for suspended monorail locomotives for underground hard coal mining operations. The BUSDUCT project envisions a suspended monorail locomotive that is powered via a busduct. With a nitrogen generator, a pressurized enclosure is formed around the area of interaction between the current collector and busduct. The HEET II project envisions a battery-powered suspended monorail locomotive which’s battery is replenished via a wireless energy transfer system that is implemented inside the monorail track. Both innovative concepts are in line with the general trend for electrification in mining (13). Thus, enhancing worker health by avoiding diesel emissions. For both projects process and environmental safety sensors are the backbone for a safe and efficient process in an underground mining environment. Both projects encounter certain difficulties from the conceptualisation to the implementation in a mining environment. One is that the proposed solutions are exemptions for the given standards for explosion protection. Once the safe operation has been demonstrated, the results of the projects may lead to amendment proposals in the standards.
6 Funding
The first part of this scientific paper was published as part of the international project BUSDUCT. This project has received funding from the Research Fund for Coal and Steel under grant agreement No 847253.
The second part of this scientific paper was published as part of the international project HEET II. This project has received funding from the Research Fund for Coal and Steel under grant agreement No 899469.
Research work published as part of an international project co-funded by the Ministry of Science and Higher Education programme entitled “PMW” in the years 2020 to 2023; contract no. 5117/FBWiS/2020/2”.
References / Quellenverzeichnis
References / Quellenverzeichnis
(1) Pieczora, E.; Tokarczyk, J. (2017): Development of mine underground transportation with use of suspended monorails. miag 4 (532), 96.
(2) Kianfar, A.; Sherikar, M.; Gilerson, A.; Skora, M.; Stankiewicz, K.; Mitra, R.; Clausen, E. (2022): Designing a Monitoring System to Observe the Innovative Single-Wire and Wireless Energy Transmitting Systems in Explosive Areas of Underground Mines 15, 576.
(3) Binnewies, M.; Finze, M.; Jäckel, M.; Schmidt, P.; Willner, H.; Rayner-Canham, G. (2016): Allgemeine und anorganische Chemie. 3rd edition, Springer Spektrum, Berlin.
(4) Nolan, D. (2014): Handbook of Fire and Explosion Protection Engineering Principles [For Oil, Gas, Chemical and Related Facilities]. 3rd edition, Elsevier, Amsterdam.
(5) Berufsgenossenschaft Holz und Metall (2013): BG-Information – Arbeitssicherheit durch vorbeugenden Brandschutz. 560th edition, Main.
(6) TRGS 727 (2017): Vermeidung von Zünd-gefahren infolge elektrostatischer Aufladung.
(7) Kissel, F. (2006): Handbook for Methane Control in Mining. Pittsburgh, PA.
(8) CEN/TR 15281:2006 (2007): Leitsätze für die Inertisierung zum Explosionsschutz. 15281st edition, Deutsches Institut für Normung e. V., Berlin.
(9) TRBS 2152 (2012): Gefährliche explosionsfähige Atmosphäre.
(10) Das Europäische Parlament und der Rat der Europäischen -Union (2014): Directive 2014/34/EU of the European Parliament and of the Council of 26 February 2014 on the harmonisation of the laws of the Member States relating to equipment and -protective systems intended for use in potentially explosive atmospheres (recast) Text with EEA relevance, 2014. Available at: https://eur-lex.europa.eu/legal-content/DE/TXT/PDF/?uri=CELEX:32014L0034&from=EN (accessed October 21, 2022).
(11) Novák, P.; Kot, T.; Babjak, J.; Konečný, Z.; Moczulski, W.; Rodriguez López, Á. (2018): Implementation of Explosion Safety Regulations in Design of a Mobile Robot for Coal Mines 8, 2300.
(12) Baack, D.; Crumbiegel, K. (1990): Erprobungseinsatz einer beweglichen schlaggwettergeschützten Stromzuführung mit schnell wirkenden Überwachungseinrichtungen für den Elektroantrieb bei Einschienenhängebahnen. Essen.
(13) Clausen, E.; Sörensen, A.; Uth, F.; Mitra, R.; Lehnen, F.; Schwarze, B. (2020): Assessment of the Effects of Global Digitalization Trends on Sustainability in Mining: Part I: Digitalization Processes in the Mining Industry in the Context of Sustainability.