Der Beitrag basiert auf einem Vortrag der Verfasser anlässlich des Aachen International Mining Symposiums (AIMS) am 27. Mai 2015.
Autoren: Dipl.-Ing. Joachim Löchte, Dipl.-Ing. Bernd Langhanki, RAG Aktiengesellschaft, Herne
Ausgangslage
Sind 100 % Wertschöpfung und Null Unfälle in Unternehmen, speziell in Bergbauunternehmen utopische Visionen, realistische Herausforderungen oder schon selbstverständliche Alltagsroutinen? Diese Frage wird im vorliegenden Beitrag von zwei Seiten beleuchtet, die vielleicht auf den ersten Blick wenige Gemeinsamkeiten aufweisen, sich in ihrer Zielrichtung sogar widersprechen. Produktivitätsgewinne auf Kosten der Arbeitssicherheit oder Effizienzverluste zu Gunsten der Arbeitssicherheit? Auf der einen Seite steht das Ziel maximale Arbeitssicherheit in allen Prozessen, also keine Gefährdung der Mitarbeiter zu jedem Zeitpunkt. Auf der anderen Seite heißt es, die maximale Effizienz in den Prozessen zuzulassen, also keine Verluste oder Verschwendungen, in keinem Prozess. Das gilt für die Produktion und für die Administration.Bei der Optimierung in beiden Themenbereichen verfügt die RAG Aktiengesellschaft (RAG), Herne, über eine langjährige Erfahrung. Dabei ist die Entwicklung im Steinkohlenbergbau Deutschlands geprägt von technischen und organisatorischen Veränderungen. Dies hat zur Folge, dass auch die Managementsysteme an die geänderten Rahmenbedingungen laufend angepasst werden. Bei diesen Entwicklungen unterscheidet sich der Bergbau nicht von anderen Industrien. Die Managementsysteme beinhalten die Vorgehensweisen und Methoden zur Erreichung von definierten Zielen im Unternehmen.
Rückblick
Um die aktuelle Zielrichtung bei der RAG zu verstehen, ist eine Rückschau auf die Entwicklungen in den letzten Jahrzehnten hilfreich. Der Bergbau in Deutschland hat sich dramatisch verändert. Das gilt aber genauso in anderen Ländern. Technisierung, Mechanisierung und Automatisierung sind die Schlagworte, mit denen diese Entwicklung charakterisiert wird. Der wesentliche unternehmerische Antrieb liegt in der Zielrichtung, die Produktivität im Unternehmen kontinuierlich zu steigern. Parallel dazu wuchsen die Anforderungen, die sich aus der Veränderung der Lagerstätte ergeben haben: Zunahme der Teufe auf bis zu 1600 m, verbunden mit negativen Auswirkungen auf das Klima und die Gebirgsdruckverhältnisse unter Tage. Auch die Ausdehnung des Grubengebäudes, entstanden durch die Entwicklung der Bergwerke in die Fläche, hat sich erheblich vergrößert. Lange Transport-, Fahrungs- und Abförderwege sind die Ergebnisse dieser Entwicklung.Die Komplexität der Prozesse und deren wechselseitige Abhängigkeiten und Beeinflussungen haben sich deutlich erhöht und zwar nicht linear zur Teufen- und Flächenentwicklung der Bergwerke, sondern exponentiell. Die Ursachen dafür sind vielfältig, so z. B. die Betriebspunktkonzentration, die Vergrößerung des Grubengebäudes, die Teufenzunahme, Entwicklungen in der Technik und in den Produktionsverfahren. Dies sind nur einige Gründe aus einem großen Spektrum. Hier liegen die Ursachen für die Einführung, ständige Anpassung und Veränderung der Managementsysteme als „Werkzeuge“ zur Unternehmensführung. Konservative, hierarchische Führungsstrukturen der ersten Entwicklungsphase im Bergbau erfüllten nicht die Anforderungen, die an die Beherrschung komplexer Unternehmensstrukturen und -prozesse gestellt waren. Dementsprechend erfolgten die Anpassungsschritte. Der vorliegende Beitrag Beitrag betrachtet die Managementsysteme zum Arbeitsschutz und zur Produktivität. Ein Managementsystem ist ein Instrument zur systematischen Umsetzung von Unternehmenszielen, also ein System als dynamisches Netzwerk von Gestaltungsprinzipien, Methoden und Werkzeugen zur Planung, zum Betrieb und zur permanenten Prozessverbesserung im Unternehmen. Diese Managementsysteme sollen Strukturen und Methoden aufzeigen als Hilfsmittel, um Prozesse und Verhalten zu standardisieren und damit nachvollziehbar und übertragbar, aber auch bewertbar und optimierbar zu machen.
Managementsysteme
Ziel des Arbeitsschutzes ist es, eine Gefährdung der Mitarbeiter unter wie über Tage in allen Prozessen vollständig zu vermeiden und damit Unfallereignisse zu verhindern. Diese Aufgabe ist im Selbstverständnis des Unternehmens weit über den gesetzlichen Rahmen hinaus verankert. Der Arbeitsschutz hatte schon immer eine große Bedeutung bei der RAG. Aber erst Anfang der 1990er Jahre wurde ein Unternehmensleitbild entwickelt, in dem Sicherheit und Produktion als gleichwertige Unternehmensziele formuliert worden sind. Die Formulierung eines Paradigmenwechsels stellte einen starken hierarchischen Impuls dar, der erhebliche Wirkung auf Organisation und Prozessgestaltung freisetzte. Unter dem Logo „AGU = Arbeits-, Gesundheit- und Umweltschutz“ ist das System in den letzten Jahren kontinuierlich entwickelt worden und hat bei der RAG eine unternehmensweite Verbreitung, Bekanntheit und Akzeptanz gefunden (Bild 1).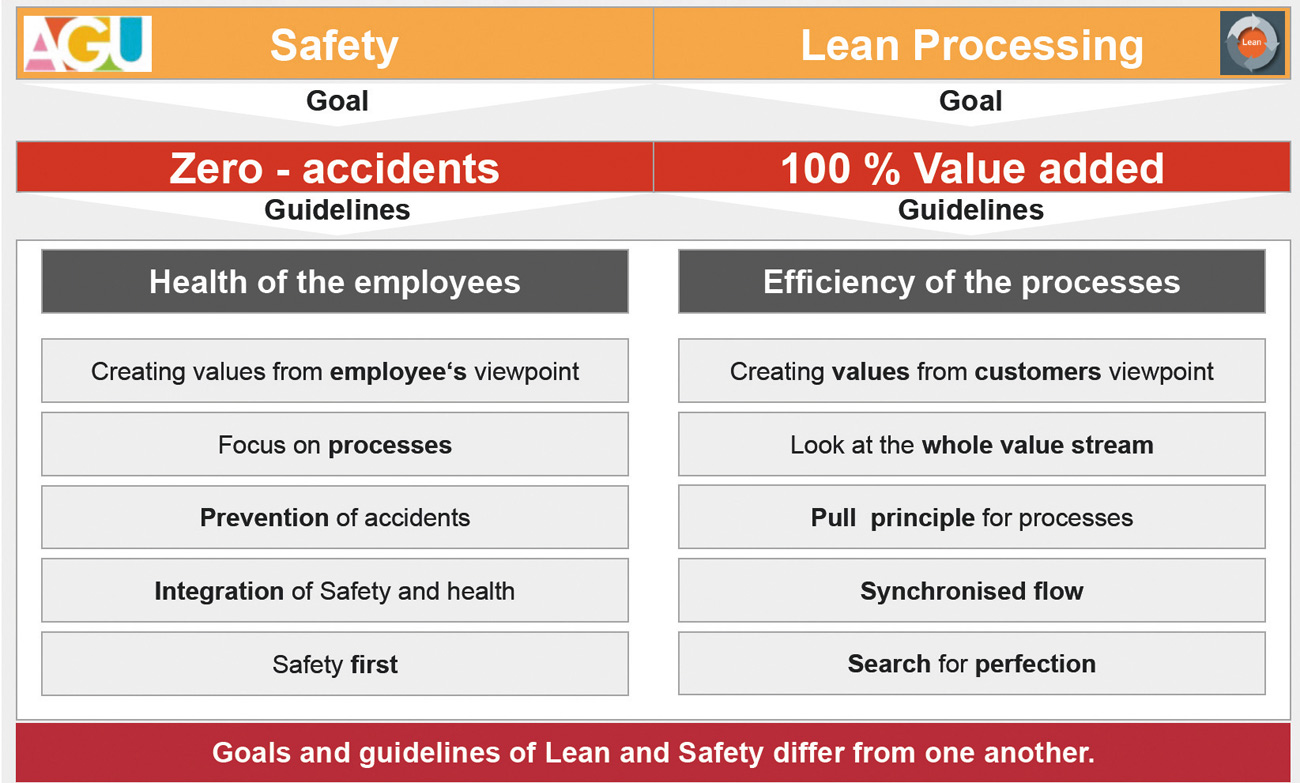
Fig. 1. A comparison of the Management systems
Bild 1. Die Managementsysteme im Vergleich
Dem Wert der Arbeitssicherheit entsprechend gelten heute im Unternehmen folgende Grundsätze:
- Die Arbeitssicherheit ist integraler Bestandteil von Planung und Betrieb.
- Für die Bearbeitung der Sicherheitsthemen werden die erforderlichen Ressourcen bereitgestellt.
- Prozesse und Zuständigkeiten werden vollständig dokumentiert.
- Ein umfassendes Berichtswesen wird gepflegt, das alle Hierarchieebenen des Unternehmens erreicht.
- Nutzung aller möglichen Kommunikationskanäle für die Arbeitssicherheit.
Die Maxime ist stets, dass alle Beschäftigten so gesund in Feierabend und Ruhestand gehen können, wie sie die Arbeit im Unternehmen aufgenommen haben. Das Ziel ist somit die Unversehrtheit der Belegschaft – null Unfälle.
Lean Processing oder kürzer Lean ist der Name des Managementsystems für die Effizienzsteigerung bei der RAG. Die Prinzipien und Ideen, die diesem Managementsystem zugrunde liegen, stammen von Toyota aus der Automobilindustrie. Werte schaffen ohne Verschwendung ist die alles entscheidende Maxime des Lean Managements weltweit. Auf den Punkt gebracht, ist das Ziel von Lean alles wegzulassen, was nicht der Wertschöpfung dient. Das gilt für alle Kern-, Führungs- und Unterstützungsprozesse im Unternehmen.
Fünf zentrale Grundsätze bilden das Grundgerüst von Lean. Sie gelten allgemein, müssen aber an die Unterschiede in den Prozessen der verschiedenen Industriezweige angepasst werden. So kann man das Lean Processing-Programm der RAG auch als Lean Mining bezeichnen.
Die fünf Grundsätze von Lean sind:
- Werte für den Kunden schaffen, d. h. Prozesse ohne Verschwendung.
- Immer den gesamten Wertstrom betrachten und nicht nur einzelne Elemente daraus.
- Wo es möglich ist, die Aktivitäten als synchronen Fluss organisieren.
- Der Kunde stößt den Prozess an (Pull-Prinzip).
- Ständiges Streben nach Perfektion, also Etablierung eines kontinuierlichen Verbesserungsprozesses.
Gefährdung vermeiden und Verschwendung eliminieren, das sind unterschiedliche Ziele im Unternehmen. Deshalb ist zu vermuten, dass sich auch die Bausteine und Erfolgsfaktoren der Managementsysteme, mit denen diese Ziele erreicht werden sollen – AGU und Lean – unterscheiden. Vielleicht kann man die These aufstellen, dass beide Managementsysteme keine oder nur wenige Gemeinsamkeiten haben und deshalb eine unterschiedliche Vorgehensweise benötigen. Im Folgenden wird gezeigt, dass dies nicht der Fall ist.
Erfolgsfaktoren der Managementsysteme
Die Entwicklung von Managementsystemen ist immer mit spezifischen Unternehmenszielen verbunden, die mit der Umsetzung der Managementsysteme erreicht werden sollen. Dabei ist zu berücksichtigen, dass allein die Einführung eines Managementsystems kein Garant dafür ist, diese Ziele nachhaltig zu erreichen. Es stellt sich also die Frage, wann die Einführung von Managementsystemen erfolgreich verläuft oder welche Faktoren bei einem Misserfolg zum Scheitern geführt haben?

Fig. 2. Success factors of Management systems
Bild 2. Erfolgsfaktoren in Managementsystemen
Aus den Erfahrungen der RAG lassen sich sechs Erfolgsfaktoren aufzeigen (Bild 2). Sie haben eine unterschiedliche Bedeutung für die nachhaltige Integration, sind virtuell in einem System verbunden und haben wechselseitige Beziehungen zueinander. Wird einer dieser Faktoren bei der Einführung, Weiterentwicklung und Stabilisierung eines Managementsystems im Unternehmen vernachlässigt, so ist das Erreichen der Ziele in aller Regel gefährdet.
Erfolgsfaktor Organisation
Für eine systemische Prozessverbesserung benötigt man Experten und methodisch geschulte Unterstützer, die qualifiziert und in der Organisation verankert werden müssen und wie interne Unternehmensberater arbeiten. Sie schulen Führungskräfte und Mitarbeiter, begleiten Verbesserungsinitiativen, Workshops, Arbeitsgruppen und stehen als Ansprechpartner mit Lean-Methodenwissen zur Verfügung. Daneben müssen Gremien und Teamgespräche etabliert werden, in denen die Umsetzung von Lean organisiert, strukturiert und weiterentwickelt wird. Diese Ablauf- und Aufbauorganisation ist quasi die „Architektur“ des Lean-Managementsystems.
Auch die Entwicklung im Arbeitsschutz zeigt die Notwendigkeit einer entsprechenden organisatorischen Verankerung. Experten für Arbeitssicherheit – Fachkräfte und Sicherheitsbeauftragte – leben das Managementsystem und entwickeln es kontinuierlich weiter. Die Verantwortung dazu trägt der Bereich Belegschaftsschutz. Mit dieser Aufbauorganisation ist AGU auf Augenhöhe mit der Produktion, der Instandhaltung und Logistik.
Es ist hervorzuheben, dass diese “Experten” für Arbeitssicherheit oder Lean als Berater zu verstehen sind. Sie tragen nicht die Verantwortung für die Arbeitssicherheit und für die Prozessverbesserung im Betrieb, sondern für die Gestaltung und Weiterentwicklung der Managementsysteme. Diese Aufgaben- und Kompetenzverteilung ist besonders in der Zusammenarbeit mit den Führungskräften von erheblicher Bedeutung.
Bei der Etablierung der Gesprächsstrukturen hat sich schnell gezeigt, dass eine gemeinsame Bearbeitung der beiden Themen zu erheblichen Synergieeffekten führt. Aus diesem Grund ist die Zusammensetzung der Gesprächskreise so verändert worden, dass sowohl der Arbeitsschutz als auch Lean durch Experten vertreten ist. Für die Mitarbeiter und Führungskräfte erfolgt die Bearbeitung somit wie aus einem Guss (Bild 3).
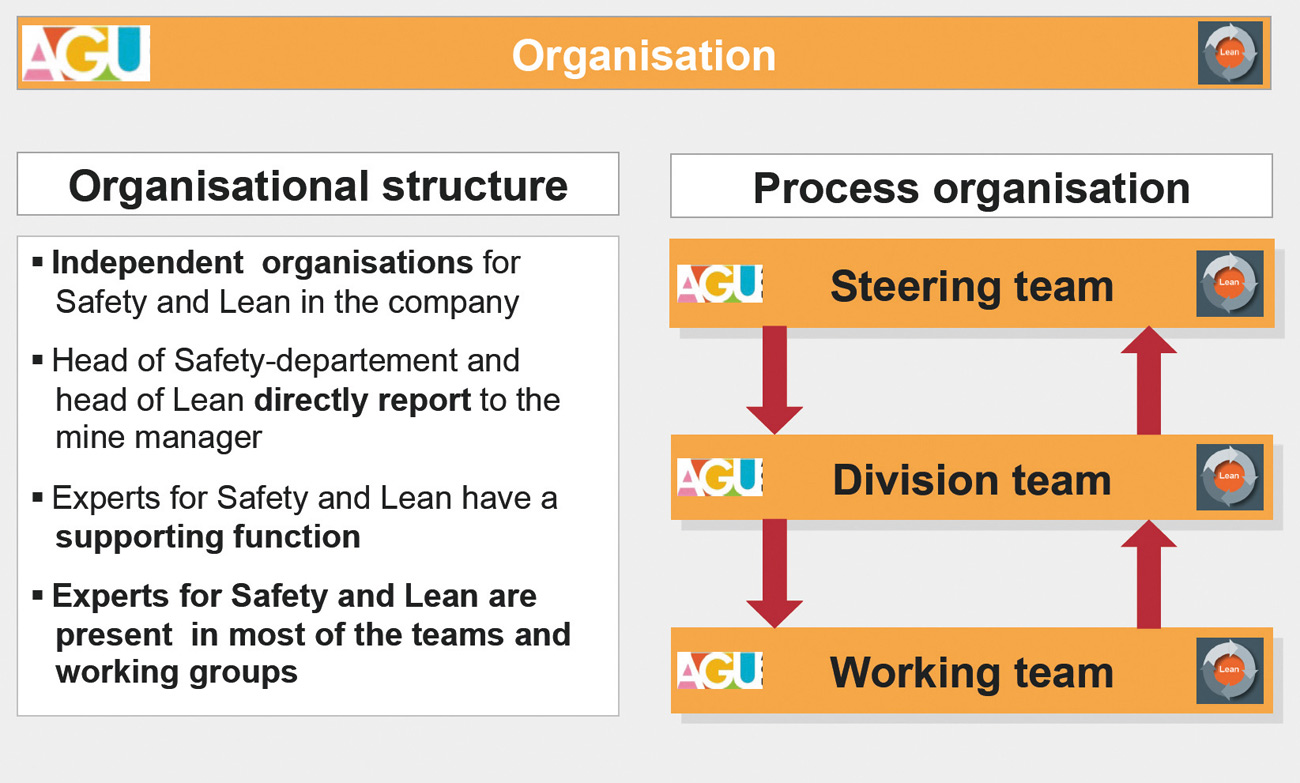
Fig. 3. Organisational structure and process organisation
Bild 3. Aufbau- und Ablauforganisation
Erfolgsfaktor Methodik
Als zweiter Erfolgsfaktor hat sich in der Arbeitssicherheit das systematische, analytische Vorgehen mit standardisierten Methoden und Werkzeugen herauskristallisiert. Ein Rückblick auf die Entwicklung bei der RAG zeigt eine starke Veränderung in der Vorgehensweise. Zu Beginn spielte insbesondere die Analyse von Unfallereignissen in einer Nachbetrachtung die entscheidende Rolle. Aus diesen Erkenntnissen wurden Maßnahmen entwickelt und betrieblich umgesetzt, die diese Ereignisse in Zukunft verhindern sollten. Dieses eher reaktive Vorgehen wurde zunehmend durch eine in die Zukunft gerichtete Sichtweise abgelöst, im Sinne eines proaktivem Vorgehens. Die heutige Zielrichtung weist darauf, Gefährdungssituationen, welcher Art auch immer, nicht entstehen zu lassen. Die richtigen Maßnahmen einzuleiten, setzt voraus, dass man die Problemstellung erkannt und verstanden hat. Erst wenn die wirklichen Ursachen für ein Problem oder eine Gefährdung analysiert sind, können wirksame Maßnahmen umgesetzt werden. Arbeitsplatz- und arbeitsprozessbezogene Gefährdungsbeurteilungen sind gesetzlich vorgeschrieben. Die Dokumentation bildet die Grundlage für die regelmäßige Information und Unterweisung aller Mitarbeiter. Visuelles Management am Arbeitsplatz, systematische Vermeidung möglicher Gefährdungen durch technische und organisatorische Maßnahmen, Trainingsbausteine zum Erkennen potentieller Gefahren sind nur einige Elemente aus dem umfangreichen Werkzeugkasten der Methoden und Werkzeuge. Diese Elemente sind Bestandteile eines kontinuierlichen Verbesserungsprozesses (KVP).
Es gibt eine Vielzahl von Methoden, die im Zusammenhang mit Lean immer genannt werden. 5S-Methode, Rüstzeitoptimierung, PDCA-Regelkreis, Wertstromdesign oder Just in time – diese Aufzählung ließe sich fortführen. Letztlich ist Lean im Ansatz pragmatisch und nutzt die Methode, die bei dem Ziel unterstützt, Verschwendung aus den Prozessen zu eliminieren. Gemeint sind Wartezeit, Doppelarbeit, Ausschuss, hohe Lagerbestände, unnötige Transporte und Bewegungen oder Überproduktion (Bild 4).
Man könnte die Methoden und Werkzeuge von Lean und AGU als die Handwerkskunst in den Managementsystemen bezeichnen, die es zu erlernen und zu beherrschen gilt. Dazu ist eine hohe Ausdauer der beteiligten Mitarbeiter und Führungskräfte erforderlich. Bei jeder methodischen Vorgehensweise entstehen Standards für Prozesse, Arbeitsabläufe, Arbeitsplatzlayouts oder das Verhalten. Selbstdisziplin und nachhaltige Umsetzung und Weiterentwicklung sind die Herausforderungen, die gemeistert werden müssen. Ein punktueller Methodeneinsatz bringt keinen anhaltenden Erfolg, das gilt für AGU und Lean gleichermaßen.
Wie bei der Organisation gibt es eine große Schnittmenge von Methoden, die gleichermaßen in der Bearbeitung von Lean und Arbeitssicherheit angewendet werden. Beispiele dazu sind die 5 S- Methode, die 5W-Fragetechnik, die Auditierung oder das visuelle Management am Arbeitsplatz (Bild 5).

Fig. 5. Methods and Tools in Management Systems
Bild 5. Methoden und Werkzeuge in den Managementsystemen
Erfolgsfaktoren Kennzahlen und Prozesssicht
Selbstverständlich muss man die Ergebnisse messen können. Kosten, Qualität und Leistung sind die Größen, auf die es ankommt, wenn es um Produktivität geht. Dabei geht der Blick über den gesamten Prozess, um nicht Optimierungen in einem Bereich zu Lasten eines anderen zu erreichen. Auch an dieser Stelle gibt es keinen Unterschied zum Arbeitsschutz. Die Dokumentation der Unfälle bzw. Ereignisse bildet die Grundlage für die Kennzahlenentwicklung. Diese hat bei der RAG einen eindrucksvollen Verlauf genommen. In den letzten 40 Jahren konnte die Unfallkennziffer (UKZ-Anzahl der Unfälle pro 1 Mio. Arbeitsstunden) von 115 auf < 5 eindrucksvoll verbessert werden (Bild 6). Damit befindet sich die RAG im Vergleich zu anderen Industriezweigen mittlerweile auf einem Spitzenplatz.

Fig. 6. Accident development in RAG’s Mining Operations
Bild 6. Unfallentwicklung im Bergbaubereich der RAG
Dieser Verlauf mit sprunghaften Verbesserungen spiegelt den Nutzen der Einführung und Weiterentwicklung des Managementsystems eindrucksvoll wider. Dies ist nicht zufällig entstanden, sondern das Ergebnis eines konsequenten, standardisierten und breit gefächerten Vorgehens im gesamten Unternehmen.
Man könnte an dieser Stelle den Eindruck gewinnen, dass die Reihe der Erfolgsfaktoren damit beendet ist. Diese These ist aber falsch. Neben den eher „technisch“ geprägten Elementen Organisation, Methodik und Kennzahlen/Prozesssicht gibt es weitere von großer Bedeutung, die die Komplexität der Managementsysteme erhöhen, aber maßgeblich zum Erfolg beitragen. Das sind die „soziologischen“ Erfolgsfaktoren Führung, Mitarbeiter und Kommunikation.
Erfolgsfaktoren Führung und Mitarbeiter
Gute Ergebnisse im Unternehmen, also eine hohe Produktivität, Qualität und Liefertreue, aber auch niedrige Unfallzahlen und geringste Gesundheitsrisiken erreicht man durch gute Prozesse. Gute Prozesse sind kundenorientiert, wirtschaftlich, sicher, optimal und schnell. Sie werden durch gute Mitarbeiter und im Zusammenwirken mit guten Führungskräften gestaltet (Bild 7).

Fig. 7. Management staff and employees in the Management System
Bild 7. Führungskräfte und Mitarbeiter im Managementsystem
Kompetente, motivierte und veränderungsbereite Mitarbeiter bilden quasi die Seele von Lean. Nur wenn es gelingt, die Mitarbeiter in die kontinuierliche, systematische Prozessoptimierung zu integrieren, mit dem Ziel, Verschwendung zu eliminieren, wird aus der Utopie 100 % Wertschöpfung eine ambitionierte, aber realistisch erscheinende Vision.
Das setzt voraus, dass die Mitarbeiter mit den Lean-Methoden vertraut sind, dass Freiräume vorhanden sind, um Prozesse systematisch zu analysieren und Verbesserungsmaßnahmen zu erarbeiten – Freiräume beispielsweise für die Teilnahme an Workshops, Arbeitsgruppenmeetings und Qualifizierungsprogrammen. Die Partizipation der Mitarbeiter basiert auf dem Grundverständnis, dass das Know-how der Mitarbeiter durch die tägliche Arbeit in den Prozessen als Expertenwissen genutzt werden muss, um schnelle, wirksame Problemlösungen zu erarbeiten und im Betrieb umzusetzen – und zwar nicht punktuell, sondern jeden Tag, an jedem Ort, in jedem Prozess.
Das gilt genauso für die Arbeitssicherheit. Die Rolle der Mitarbeiter hat sich im Laufe der Jahre erheblich verändert. Noch vor 40 Jahren waren Unternehmen geprägt durch eine klassisch-hierarchische Führungskultur. Der Mitarbeiter bewegte sich in engen Grenzen. Durch Anweisung und Überwachung wurde die Arbeitssicherheit umgesetzt. Dies, gemeinsam mit der Entwicklung der Technik, hat in diesem Stadium der Unternehmenskultur bereits zu sprunghaften Verbesserungen geführt. Ein hierarchischer Eingriff konnte noch positive Wirkung entfalten.
Wie man heute weiß, erfordert ein höherer Anspruch aufgrund eines bereits erreichten besseren Niveaus eine intensivere und bessere Mitwirkung der Beschäftigten (Bild 8), weil die hierarchische Wirkung in dieser Organisationsphase begrenzt ist (1). Die Beseitigung der gröbsten Fehlerereignisse ist zunächst durch bloße hierarchisch-autoritäre Eingriffe möglich. Nachdem die großen Hindernisse beseitigt sind, wird ein gestaltendes Mitwirken der einzelnen Mitarbeiter und später auch von eigenverantwortlichen Mitarbeiterteams Erfolg bestimmend. Von dieser Stufe bzw. von diesem Zeitpunkt an ist die hierarchische Wirkung begrenzt. Mit Ereignissen sind hier zunächst Unfallereignisse gemeint. Aber auch für die Verschwendungsereignisse in Produktionsprozessen gilt, dass eine weitere Verbesserung erst durch die umfassende Einbindung der Mitarbeiter zu erreichen ist. Der dazu notwendige Wandel der Unternehmenskultur erfolgt nicht von selbst, sondern muss aktiv gestaltet werden.
Man weiß zudem, dass heute mehr als 90 % der Unfälle – damit sind alle Ereignisse gemeint, auch die ohne Ausfallzeit – verhaltensbedingt und nicht auf technische Unzulänglichkeiten zurückzuführen sind. Demzufolge war es notwendig, mit Maßnahmenschwerpunkten in der Unfallprävention auf organisatorische und persönliche Aspekte zu zielen. Verhalten und Einstellung der Mitarbeiter in die Richtung „Null Ereignisse ist das Ziel“ zu verändern, darin liegt die Herausforderung, um immer besser zu werden. Aber Verhalten und Einstellung verändern sich nicht von allein, sondern dies ist ein langer Weg mit zahlreichen Wegpunkten. Man benötigt eine große Ausdauer bei Führungskräften und Mitarbeitern. Die hierzu notwendige Motivation erreicht man durch Trainings zur Gefährdungsbeurteilung, durch Qualifizierungsmaßnahmen, in Audits zur Sicherheit und mit Lob und Tadel in Gesprächen. Mitverantwortung durch Partizipation wird ein wesentlicher Baustein der Unternehmenskultur.
An dieser Stelle ist man am gemeinsamen Punkt von erfolgreicher und nachhaltiger Verbesserung der Arbeitssicherheit und Lean-Implementierung im Unternehmen. Mitarbeiter und Führungskräfte sind wesentliche, wenn nicht sogar die wesentlichen Erfolgsfaktoren in einem Managementsystem. Gelingt es, beide für Lean und AGU zu begeistern und aktiv an der Gestaltung und Weiterentwicklung zu beteiligen, ist das Erreichen ambitionierter Ziele eher möglich. Dabei wird unterstellt, dass die Mitarbeiter die Prozesse, die Sie ausführen, am besten kennen. Natürlich kennen Sie damit auch die Probleme, Gefährdungen und Verschwendungen, die täglich auftauchen. Deshalb ist es Aufgabe der Führungskräfte, die Mitarbeiter am kontinuierlichen Verbesserungsprozess zu beteiligen und dabei zu coachen. Die Führungskräfte sind in der Rolle eines „Lotsen“ und die Mitarbeiter bilden die eigentliche „Seele“ der Managementsysteme.
Erfolgsfaktor Kommunikation
Ein weiterer wichtiger Erfolgsfaktor, die Kommunikation, rundet das Gesamtbild ab. Sie bildet quasi das „Schmiermittel“ des Managementsystems. Die Bedeutung der Arbeitssicherheit für die RAG wird durch eine vielfältige, ständige und zielgerichtete Kommunikation im Unternehmen, im Betrieb und vor Ort herausgestellt. Beiträge im Mitarbeiter-Magazin, Aktionen, Ausstellungen und Aktionstage schaffen Aufmerksamkeit und unterstützen die Zielerreichung in der Arbeitssicherheit. Besondere Bedeutung haben die Gespräche der Mitarbeiter untereinander, mit Fachleuten für Arbeitssicherheit und natürlich mit den Führungskräften. Damit erreicht man, dass Sicherheit bei der Arbeit zur Routine, zum Tagesgeschäft wird und die Zusammenarbeit im Team unter wie über Tage prägt (Bild 9).
Im Vergleich mit Lean sind keine Unterschiede zu erkennen, die Forderungen an die Kommunikation sind vollständig übertragbar. Auch bei Lean geht es darum, die systematische Prozessverbesserung als Tagesgeschäft zu verstehen und nicht als Zusatzaufgabe parallel zur Arbeitsroutine. Dabei stützt sich die Kommunikation auf verschiedene Säulen. Eingesetzte Medien unterstützen die „Vermarktung“ der Themen im Unternehmen, z. B. die Mitarbeiterzeitung „Steinkohle“, das Intranet und Flyer. Aktionen in den Betrieben, Unternehmensforen, AGU- und Lean-Tage schaffen weitere Aufmerksamkeit für die Themen und bieten gleichzeitig eine Plattform zum Austausch von Informationen und guten Erfahrungen. Als dritte und wichtigste Säule ist das persönliche Gespräch zwischen den Mitarbeitern und den Führungskräften anzusehen. Hier wird Arbeitssicherheit und Prozessverbesserung am Arbeitsplatz thematisiert und spezifisch auf die jeweilige Situation ausgerichtet. Die Anforderungen, die dabei an die Führungskräfte gestellt werden, können nicht als Selbstverständlichkeit vorausgesetzt werden. Training und Qualifizierung der Führungskräfte sind notwendig, um das geforderte Verhalten und die erforderliche Einstellung zur Routine zu machen.
Synergien durch Integration der Managementsysteme
Aus der Betrachtung der Erfolgsfaktoren wird deutlich, dass bei der RAG die Managementsysteme für die Arbeitssicherheit und für Lean große Schnittmengen aufweisen und durch die gemeinsame Bearbeitung erhebliche Synergien entstehen:- Das ganze Unternehmen „atmet“ Lean und Arbeitssicherheit. Ein tiefes Verständnis ist vorhanden und die erforderlichen Denk- und Verhaltensweisen bei den Führungskräften und Mitarbeitern sind zu beobachten.
- Das ganze Unternehmen lernt auf beiden Gebieten täglich hinzu, das Niveau steigt ständig.
- Verbesserung ist Tagesgeschäft, auftretende Probleme werden rasch und nachhaltig gelöst.
- Es besteht eine Kultur der kontinuierlichen Verbesserung. Lean und Arbeitssicherheit sind untrennbar verbunden.
- Das Denken in Arbeitssystemen prägt die Zusammenarbeit.
- Die Orientierung an den Zielen und der daraus abgeleiteten Strategie des Unternehmens lassen sich in kleinsten Prozessschritten erkennen. Mitarbeiter und Führungskräfte haben das verinnerlicht.

Fig. 10. Successful Example of integrated Approach – Lean & Safety
Bild 10. Erfolgreiches Beispiel der integrativen Bearbeitung – Lean & Arbeitssicherheit
Ein gutes Beispiel für eine solche integrative Bearbeitung der Themen aus der jüngeren Vergangenheit ist die Vorbereitung von Herrichtung und Gewinnung im Flöz Zollverein des Bergwerks Prosper-Haniel (Bild 10). In einer 25 m langen, realitätsnah ausgestatteten Übungsstrecke über Tage machte sich die Mannschaft, die später die Montage und den Betrieb durchführt, mit dem Equipment vertraut (2). Alle Arbeitsschritte wurden mehrfach realitätsnah durchgeführt und optimiert. Das Ergebnis waren effiziente und sichere Arbeitsprozesse.
Die integrative Bearbeitung beider Themen ist mittlerweile bei der RAG gut gepflegt. In den regelmäßigen Gesprächskreisen und Teamsitzungen der Betriebe stehen sie im Vordergrund. Die konsequente Thematisierung auf allen Ebenen des Unternehmens gewährleistet, dass Lean und Arbeitssicherheit nicht als Zusatzaufgaben zur Arbeit der Planung und Steuerung des Betriebes aufgefasst werden, sondern wie selbstverständlich dazugehören. Es herrscht die feste Überzeugung, dass man die positive Wirkung auch an der Entwicklung der Unfallkennziffer in den letzten 10 Jahren ablesen kann, ohne dass sich diese Wechselwirkung unmittelbar nachweisen lässt. Die Veränderung der Unternehmenskultur hat eine gegenseitige Befruchtung von Lean und dem Umgang mit der Arbeitssicherheit bewirkt. Dass z. B. Abbau und Vorleistungsbetriebe über Monate unfallfrei geblieben sind, wäre noch vor wenigen Jahren als unmöglich angesehen worden. Diese Erfolge sind noch nicht selbstverständlich, aber auch nicht mehr utopisch. Sie sind das Ergebnis konsequenter, kontinuierlicher und kooperativer Arbeit.
Mit drei Fragestellungen kann man diesen Wandel nachvollziehen.
- Sehen die Mitarbeiter und Führungskräfte Verbesserung als festen Bestandteil, Arbeit oder Zusatzaktivität zum eigentlichen Job an?
- Ist Verbesserung in Lean und AGU ein periodisches Zusatzprodukt, eine Kampagne oder die zentrale Aktivität?
- Wird es im Unternehmen akzeptiert, nur gelegentlich an Verbesserungen zu arbeiten?
In der Beantwortung dieser Fragestellungen liegt der Schlüssel zum Erfolg. Erst wenn es gelingt, Prozessverbesserung – und das bezieht sich auf alle Zielgrößen wie Effizienz, Qualität, Sicherheit und Wirtschaftlichkeit – als permanente tägliche Aufgabe zu verstehen, sind auch utopisch erscheinende Zielzustände realisierbar.
Fazit
Bei der RAG ist die Steigerung der Produktivität und der Arbeitssicherheit kein Widerspruch. Vielmehr müssen beide Ziele und die dazugehörigen Managementsysteme als Beiträge zur Vermeidung von Verschwendung gesehen werden. Auf dem Weg des Unternehmens mit immer schwierigeren Rahmenbedingungen konnten Potentiale gehoben werden. Eingeleitet durch das Bekenntnis zur Gleichrangigkeit von Produktion und Arbeitssicherheit fand ein Kulturwandel von einer hierarchisch autoritären zu einer integrativen Führungskultur statt, der es heute gestattet, Prozesse wirkungsvoll unter Beteiligung der Beschäftigten zu planen und zu optimieren. Offener Umgang, Teamfähigkeit, Verantwortungsbewusstsein und Achtsamkeit sind Ausdruck dieser Kultur. Hierdurch gelingt es, die Erfahrung der Mitarbeiter als Expertenwissen zu nutzen und die Erfolgsfaktoren für die der Optimierung zugrunde liegenden Managementsysteme voll zur Wirkung zu bringen. Diese Erfolgsfaktoren sind Organisation, Methodik, Prozesssicht und Kennzahlen, Führung und Mitarbeiter sowie die Kommunikation.References / Quellenverzeichnis
References / Quellenverzeichnis
(1) Remo Küry, ABB: Grundlagenentwicklung nach Bradley: http://www.netzwerk-risikomanagement.org/uploads/media/Netzwerk_RM_2013-03-14.pdf
(2) Becker, M., Martin, P., Junker, M.: Intelligente Strebsysteme für den internationalen Steinkohlenbergbau mit Anbindung an moderne Wartensysteme. Mining Report Glückauf (151), Heft 5/2015, S. 386-394
Autoren: Dipl.-Ing. Joachim Löchte, Dipl.-Ing. Bernd Langhanki, RAG Aktiengesellschaft, Herne