1 Einführung
Kann VISION ZERO im Nicht-Kohle-Bergbau ein realistisches Ziel sein? Die Frage ist aufgrund entsprechender Erfahrungen eindeutig mit „Ja“ zu beantworten. Aber zunächst ein paar generelle Hinweise.
VISION ZERO ist nicht nur ein Ziel, sondern auch Bestandteil der Präventionsstrategie in einem nationalen Arbeitssicherheitsprogramm und im jeweiligen Industrieprogramm. Man muss sich darüber klar werden, dass Arbeitsunfälle und Berufskrankheiten keine Zufallsereignisse sind oder nur auf Fehlverhalten von Mitarbeitern beruhen. Es ist die generelle Verantwortung des Managements, Unfälle und Berufskrankheiten zu vermeiden. Das Management hat alle zur Umsetzung von VISION ZERO erforderlichen Maßnahmen zu ergreifen. Bevor man irgendwelche diesbezüglichen Maßnahmen ergreift, muss man sich allerdings im ersten Schritt über seine Ausgangslage klar werden und eine realistische Bestandsaufnahme durchführen.
Nachfolgend einige Beispiele einer Bestandsaufnahme.

Fig. 1. Excavator in front of debris after very bad blasting result. // Bild 1. Bagger vor Haufwerk nach sehr schlechtem Sprengergebnis. Photo/Foto: Peter Rödel
Bild 1 zeigt Haufwerk nach sehr schlechtem Sprengergebnis und mit vielen Knäppern, die zu Problemen beim Laden, Transportieren und in der Vorzerkleinerung führen werden. Darüber hinaus existiert kein sicherer Kabinenzugang auf dem Bagger. Es gibt also zwei Bereiche mit dringendem Handlungsbedarf: Die Bohr- und Sprengtätigkeit sowie die sicherheitstechnische Ausrüstung der Geräte.

Fig. 2. Unsuitable wheel loader in a quarry. // Bild 2. Ungeeigneter Radlader in einem Steinbruch. Photo/Foto: Peter Rödel
Bild 2 zeigt einen Radlader ohne Roll Over Protecting Structures (ROPS), Falling-Object Protecting Structures (FOPS) und ohne Schutzgitter für die Frontscheibe. Weiterhin ist dieses Gerät zu klein, um das im Bild gezeigte Haufwerk zu laden. Der Radlader wird sich beim Anheben der Knäpper hinten hochstellen. Die Standsicherheit ist nicht mehr gewährleistet, und das nächste Schadensereignis ist somit absehbar.

Fig. 3. Poorly maintained wheel loader. // Bild 3. Mangelhaft gewarteter Radlader. Photo/Foto: Peter Rödel
Die Bilder 3 und 4 bedürfen eigentlich keines weiteren Kommentars. Man sieht in diesem Betrieb sehr große Probleme in vielen Betriebsbereichen – vom Steinbruch über die Werkstatt bis hin zur Spannungsversorgung. Unter solchen Umständen sollte sich niemand über Arbeitsunfälle und unzuverlässige Produktionsbedingungen wundern.

Fig. 4. Inadequate repair of the power supply of a drill. // Bild 4. Unzureichende Reparatur der Spannungsversorgung eines Bohrgeräts. Photo/Foto: Peter Rödel
2 Null Unfälle im Nicht-Kohle-Bergbau – eine Fallstudie
Nachfolgend wird von einem europäischen Steinbruch berichtet, der eine Zementklinkerproduktionsanlage in einer Entfernung von > 1 km mit Rohstoff versorgt. Aufgrund dieser Stand-alone-Situation und in Verbindung mit den Zielen von VISION ZERO wurden in dem Steinbruch sehr intensiv Gefährdungsanalysen durchgeführt, mit der Absicht, das Ziel „Null Unfälle“ zu erreichen.
Die Gefährdungsanalysen wurden nicht nur für den bestimmungsgemäßen Betrieb, sondern auch für Reparatur- und Abbrucharbeiten in den Bereichen Abbauplanung, Bohren und Sprengen, Laden und Fördern, Zerkleinerung, Instandhaltung und Sozialbereich, Gefährdungen durch Strom, Staub und Arbeit in großer Höhe sowie weiteren gefährlichen Tätigkeiten mit den nachfolgend beschriebenen Ergebnissen durchgeführt.
2.1 Abbauplanung
Die geologische Situation ist recht einfach. Abgebaut wird ein Jura-Kalkstein im sogenannten Pariser Becken. Es handelt sich um eine ungestörte Sedimentablagerung, die keine besonderen Maßnahmen aufgrund von Einfallen und Streichen im Rahmen der Abbauplanung erfordert. Damit kann man sich auf die Höhe der Strossen, die zwischen 10 und 12 m variiert, konzentrieren. Das ist in Anbetracht der eingesetzten Radladergröße eine komfortable Höhe. Der Radlader ist in der Lage, die Wand bis zu einer Höhe von ca. 7 m von losem Material zu beräumen.
2.2 Bohren und Sprengen
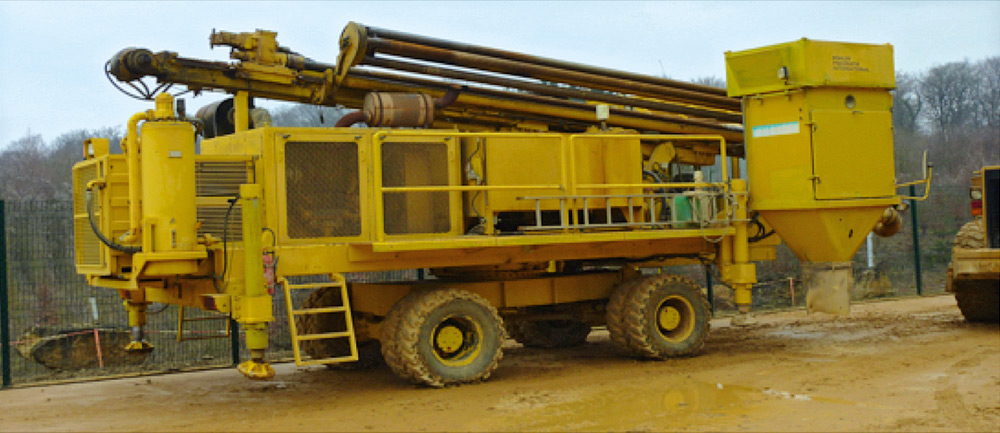
Fig. 5. The extraction is done by means of two Boehler TC 222-drilling rigs. // Bild 5. Für die Bohrarbeit werden zwei Boehler-TC 222 Geräte eingesetzt. Photo/Foto: Peter Rödel
Die Gefährdungsanalysen zum Bohren (Bild 5) kamen zu folgenden Ergebnissen:
Der Bohrgeräteführer ist auf einem Einzelarbeitsplatz tätig. Um mit seinem Schichtführer und/oder seinen Kollegen in Kontakt zu bleiben, verfügt er über ein Sprechfunkgerät zu seiner persönlichen Disposition. Ein „externer“ Kollege ist verpflichtet, mehrmals und regelmäßig pro Schicht Kontakt mit dem Bohrgeräteführer aufzunehmen. Zur Vermeidung von Unfällen mit anderen Geräten bzw. Fahrzeugen sind die Arbeitsbereiche der Bohrgeräte mit großen Steinblöcken abgesichert. Rotierende Signalleuchten verbessern die Wahrnehmung der Geräte.
Zur Vermeidung von Unfällen durch Steinfall aus der Wand verfügen die Kabinen über eine FOPS-Sicherheitsausrüstung.
Nur dazu befugte Mitarbeiter dürfen mit Sprengstoff und Zündern entsprechend den staatlichen Vorschriften und den Betriebsanweisungen umgehen. Zur Gewährleistung eines maximalen Sicherheitsniveaus im Hinblick auf die Vermeidung von Steinflug und zur Minimierung von Sprengerschütterungen gelangen nicht-elektrische Zünder zur Anwendung.
2.3 Ladearbeit
Bezüglich der Gefährdungsanalysen für die Ladearbeit mittels Radlader (Bild 6) sind zwei wichtige Punkte herauszustellen.

Fig. 6. Loading is done by a CAT 990-wheel loader, operating weight 78 t, payload 15 t, 650 hp. // Bild 6. Ein Radlader CAT 990 mit einem Dienstgewicht von 78 t, einer Nutzlast von 15 t und 650 PS Antriebsleistung übernimmt die Ladearbeit. Photo/Foto: Peter Rödel
Der erste Punkt betrifft die Gefahr von Steinfall aus der Wand. Nach einer Sprengung und vor Aufnahme der Ladetätigkeit muss eine Überprüfung des Haufwerks durchgeführt werden. Wenn eine Gefährdung erkannt wird, die nicht mit dem Radlader beseitigt werden kann, ist der Schichtführer zu informieren, damit dieser eine Beräumung der Ladestelle organisiert.
Die andere gravierende Gefährdung ist der Betrieb des Radladers zu nahe an einer darunter liegenden Abbauwand. Diese Gefährdung wird dadurch vermieden, dass die Geräte nicht näher als 5 m von der Abbaukante betrieben werden. Die Abbauführung ist so zu gestalten, dass die hierfür erforderliche Sohlenbreite immer gewährleistet ist.
2.4 Förderung
Die Gefährdungsanalysen für die Förderung hatten u. a. zum Ergebnis, dass der Individualverkehr im Steinbruch eines der größten Risiken darstellt.

Fig. 6. Loading is done by a CAT 990-wheel loader, operating weight 78 t, payload 15 t, 650 hp. // Bild 6. Ein Radlader CAT 990 mit einem Dienstgewicht von 78 t, einer Nutzlast von 15 t und 650 PS Antriebsleistung übernimmt die Ladearbeit. Photo/Foto: Peter Rödel
Wegen der Kollisionsgefahr zwischen Lade- und/oder Fördergeräten (Bild 7) müssen die Geräteführer jährlich einen medizinischen Check und eine Geräteführerprüfung absolvieren. Zur Gefährdungsreduzierung während des Ladens bzw. Förderns sind die Geräte mit Sicherheitseinrichtungen wie Sicherheitsgurten, Rückfahrwarneinrichtungen, ROPS-Kabinen, verbesserten Zugängen u. ä. ausgerüstet. Zur Vermeidung von Staubemissionen und schlechter Sicht durch Staub werden die Straßen regelmäßig befeuchtet. Bei Glatteis wird Salz auf die Transportwege gestreut. Große Gesteinsblöcke (Knäpper) sichern die Förderstrecken seitlich ab (Bild 8).

Fig. 8. Big stone blocks between hauling road and slope edge. // Bild 8. Knäpper zur seitlichen Absicherung der Förderstrecken gegen Absturz auf die untere Sohle. Photo/Foto: Peter Rödel
Zur Vermeidung von Risiken durch Steinfall aus der Wand ist es verboten, näher als 5 m an die Abbauwände heranzufahren. Um Gefährdungen durch Glatteis, Nebel, Regen oder schlechte Sicht zu vermeiden, sind die Straßen in diesem Tagebau durch fluoreszierende Randmarkierungen gesichert (Bild 9). Regelmäßige Unterhaltungsarbeiten an den Förderstraßen sind ebenso wichtig wie das Salzen der Kurven in Frostperioden.
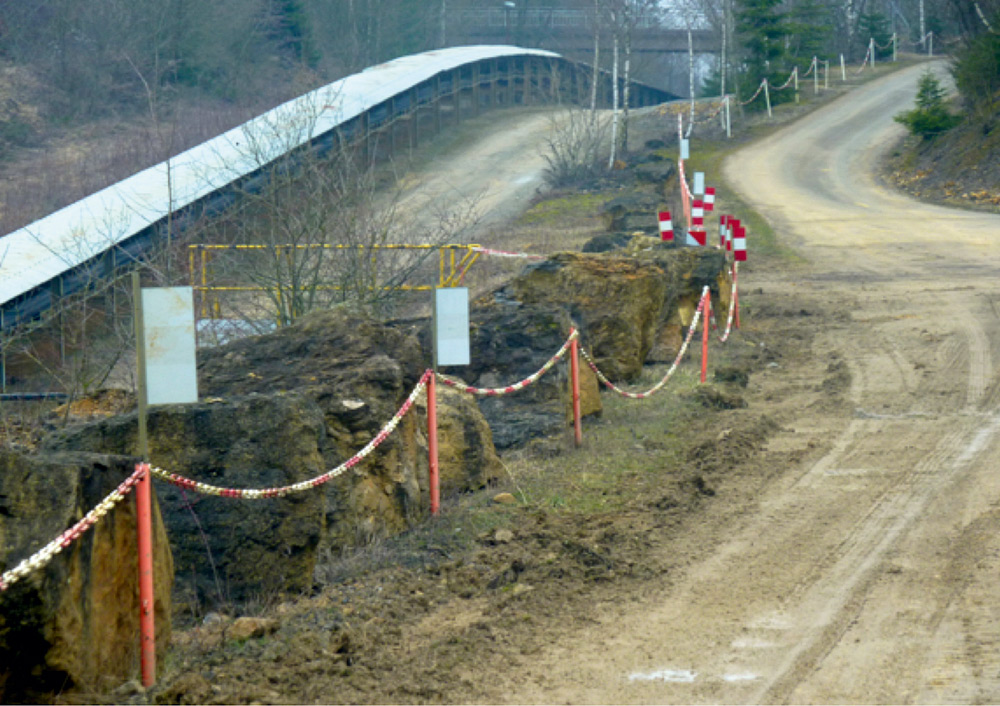
Fig. 9. Fluorescenting road signs as an example of good practice. // Bild 9. Fluoreszierende Randmarkierungen entlang der Förderstrecken. Photo/Foto: Peter Rödel
2.5 Vorbrecher
Die Gefährdungsanalyse bezüglich der Primärzerkleinerung wurde mit folgenden Ergebnissen durchgeführt.

Fig. 10. Arbed twin hammer crusher for milling the limestone down to max. 200 mm. // Bild 10. Arbed-Doppelwellenhammerbrecher zur Vorzerkleinerung des Kalksteins auf max. ca. 200 mm. Photo/Foto: Peter Rödel
Besonders hervorzuheben ist das Risiko des Hineinfallens/Hineinrutschens in den Abkippbunker vor der Beschickungseinrichtung des Brechers (Bild 10). Dies wurde in der Betriebsanweisung berücksichtigt, die eine Begehung dieses Bereichs während des Vorbrecherbetriebs ausdrücklich verbietet. Die erforderliche Kontrolle der Situation kann von einer gesicherten Plattform oberhalb des Vorbunkers bzw. über Kamera und Monitor im Leitstand des Brechers erfolgen. Als weitere Gefährdung wurde der Verkehrsbereich der SLKWs rund um den Vorbrecher erkannt. Er wird mittels Kette abgesperrt und ist mit einem Sicherheitszeichen gekennzeichnet. Als Schutz gegen Steinflug aus dem Brecher darf die Bedienung nur aus der Leitstandskabine erfolgen, die schallgeschützt und schwingungsgedämpft sowie mit einer Klimaanlage ausgerüstet ist.
2.6 Besondere Gefährdungen
Hier wurden insbesondere Gefährdungen durch Strom, Staub, Arbeiten in großer Höhe u. ä. mit den folgenden Konsequenzen untersucht:
- Jedes Belegschaftsmitglied muss alle allgemein gültigen Regeln und Vorschriften des Werks und speziell die des Steinbruchs beachten.
- Neue Mitarbeiter und externe Kontraktoren müssen sich vor Aufnahme ihrer Arbeit einer umfassenden Unterweisung zum Arbeits- und Gesundheitsschutz unterziehen und die Teilnahme bestätigen lassen. Weiterhin erhalten sie eine Broschüre mit einem Überblick von allen Sicherheitsvorschriften, werksinternen Verhaltensregeln und den wichtigsten Telefonnummern.
- Zur Vermeidung von Pneumokoniose werden – wann immer nötig – die Förderstraßen und auch die Ladebereiche sowie der Abkippbunker am Vorbrecher befeuchtet. Alle Kabinen der SLKWs, Radlader, Bohrgeräte und des Vorbrechers sind mit Klima-anlagen ausgerüstet.
- Vorbrecher und Bohrgeräte sind mit sehr leistungsfähigen Schlauchfilteranlagen ausgerüstet.
- Bei Arbeiten unter Staubeinwirkung muss der zur persönlichen Schutzausrüstung gehörende Staubfilter getragen werden. Die Teilnahme an der jährlichen arbeitsmedizinischen Vorsorgeuntersuchung ist obligatorisch.
- Alle Arbeiten in großer Höhe werden grundsätzlich von Arbeitsplattformen mit Handläufen ausgeführt. Wo dies nicht möglich ist, kommen Arbeitsbühnen oder spezielle Sicherheitsgeschirre zur Anwendung.
- Gefährliche Arbeiten dürfen nur nach Erteilung einer schriftlichen Genehmigung vom Hauptsicherheitsingenieur durchgeführt werden. Diese Genehmigung enthält die Informationen über alle Risiken der gefährlichen Arbeit und die zu ergreifenden Sicherheitsmaßnahmen.
2.7 Weitere Maßnahmen
Es ist offensichtlich, dass die intensiven Gefährdungsanalysen nicht die einzigen Maßnahmen auf dem Weg zu VISION ZERO sein können, denn auf dem Weg dorthin sind die Mitarbeiter von enormer Wichtigkeit. Deshalb ist es von großer Bedeutung, sich u. a. gemäß den 7 Goldenen Regeln von VISION ZERO um seine Mitarbeiter zu kümmern, d. h. in die Belegschaft zu investieren sowie die Mitarbeiter zu trainieren und zu motivieren. Was heißt das für die o. g. Fallstudie?
Der Betriebsleiter des Steinbruchs hat eine externe Qualifikation von sechs Monaten absolviert und ist zu allen Themen und Fragen des Steinbruchbetriebs wie Sicherheit beim Bohren und Sprengen, Gebirgsmechanik sowie Radlader- und SLKW-Betrieb ausgebildet worden. Die beiden Sprengberechtigten haben eine Ausbildung unter staatlicher Aufsicht zum Umgang mit Sprengstoff und Zündern absolviert. Diese Qualifikation muss jährlich erneuert werden. Jeder Fahrer eines Radladers oder SLKWs sowie die Mitarbeiter in der Werkstatt haben eine speziell auf die von ihnen betriebenen und gewarteten Geräte abgestimmte Ausbildung in einem Trainingscenter des Geräteherstellers absolviert. Diese Trainings müssen jährlich wiederholt werden.
Für die Belegschaft aus der Fallstudie ergeben sich aus diesen Aufwendungen folgende Vorteile:
- Sie arbeitet seit mehr als 20 Jahren unfallfrei. Unfall bedeutet in diesem Fall den Besuch eines Arztes nach einer Verletzung bei der Arbeit. In Asien findet man Unfalldefinitionen, die von Unfallfreiheit bei bis zu 200 Ausfalltagen sprechen.
- Sie arbeitet mit höherer Produktivität als andere Steinbrüche aufgrund der besseren Kenntnis der durchzuführenden Tätigkeiten – auch im Management – infolge der intensiven Gefährdungsbeurteilungen und aufgrund einer besseren Motivation.
- Sie arbeitet mit höherer Geräte- und Anlagenverfügbarkeit bei geringeren Betriebskosten.
- Sie arbeitet im Beispielbetrieb mit ca. 50 % niedrigerer Ausfallzeit im Vergleich zum Durchschnitt der vergleichbaren Betriebe.
In kritischen Situationen – bei einem Brand, nach einem Unfall o. ä. – zeigt sich immer wieder sehr schnell, wie gut oder schlecht die Verantwortlichkeiten in einem Betrieb geregelt sind und von den Mitarbeitern wahrgenommen werden. Vielfach ist eine mangelhafte oder fehlende Sicherheitskultur Ursache dafür, dass man das Ziel von VISION ZERO nicht erreicht.
Dazu ein paar theoretische Anmerkungen:
Sicherheit wird häufig als ein Zustand definiert, in dem die verbleibenden Risiken als akzeptabel eingestuft werden und das meistens auf der Basis der Unfallhäufigkeit. Aber diese Definition leitet sich häufig nur aus der Vergangenheit ab und basiert auf einer mehr oder weniger persönlichen Meinung oder allgemeinem Konsens.
Es scheint aber deutlich vorteilhafter zu sein, Sicherheit als einen zu optimierenden Prozess mit menschlichen Wesen, mit Technologie und lebendigen Organisationsstrukturen zu verstehen. Dieser Prozess muss wichtiger Bestandteil der Sicherheitskultur sein. Diese und das Sicherheitsklima sind sehr wichtige Faktoren, die Nützlichkeit und Verhaltensregeln beinhalten. Die richtige Wahrnehmung und die Einschätzung der Gefährlichkeit einer Situation durch den Mitarbeiter sind unabdingbar für die Vermeidung von Unfällen.
Warum passieren Unfälle? Man muss sich darüber klar werden, dass Unfälle nicht durch einen einzelnen Fehler einer einzelnen Person verursacht werden, sondern Teil einer Serie von Fehlern sind. Diese Fehler sind Teil einer individuellen Situation innerhalb einer Belegschaft.
Dieses äußerst schwierige Problem lässt sich durch Investitionen in die Belegschaft, durch Erzeugen von Stolz auf ihre Arbeit und durch Motivation lösen. VISION ZERO ist also nicht nur eine Frage von Gesetzen und Vorschriften, sondern es hat sehr viel mit Menschen und deren Zusammenwirken mit der Technik zu tun. VISION ZERO ist ein dynamischer Prozess, der immer wieder an die aktuelle Entwicklung angepasst werden muss. Er erfordert, dass man seine Belegschaft mitnimmt. Wenn man sie überzeugt hat, wird VISION ZERO nachhaltige Realität.
3 Präventionskultur in der Praxis
Vielfach wird argumentiert, dass es einen Widerspruch zwischen den Zielen von Arbeits- und Gesundheitsschutz einerseits und den Zielen der Produktion andererseits gäbe. Das ist dann richtig, wenn VISION ZERO nur oberflächlich verfolgt wird. Aber wenn der Ansatz grundsätzlich und ehrlich ist, wird man nicht nur eine moralische Verpflichtung erfüllen, nach Recht und Gesetz leben und Sicherheitsvorschriften einhalten. Erinnert sei in diesem Zusammenhang auch an die „gerichtsfeste Organisation“. Man wird die Effizienz steigern sowie eine höhere Produktionsrate und -qualität bei niedrigeren Herstellkosten erreichen aufgrund der besseren Vorbereitung der Prozesse, die man für umfassende Gefährdungsanalysen immer benötigt.
Bei diesen ehrgeizigen Zielen darf man neben allen Gesetzen und Vorschriften nicht vergessen, dass die wichtigsten Voraussetzungen für das Erreichen der Ziele von VISION ZERO im Tagesgeschäft die Sicherheitskultur in einer Organisation und das Sicherheitsbewusstsein in den Köpfen der Mitarbeiter sind.
4 Empfehlungen
Zum Ziel von VISION ZERO gehören unbedingt entsprechende Arbeitsbedingungen. PPE, Licht am Arbeitsplatz, Werkzeug, Sitze, Bildschirme, regelmäßige Untersuchungen durch einen Arbeitsmediziner usw. sind essentiell.
Allen Zweiflern von VISION ZERO muss man entgegnen, dass das Erreichen der Ziele sich durch bessere Motivation der Mitarbeiter, höhere Produktivität, eine geringere Fehlerrate sowie eine bessere Anlagenverfügbarkeit bezahlt macht. Arbeits- und Gesundheitsschutz sind ähnlich zu sehen wie das Staubwischen zu Hause – man muss es jeden Tag auf´s Neue tun. Daher ist es wichtig,
- die Mitarbeiter davon zu überzeugen, dass sichere Arbeit ein Beleg für eine hohe Qualität ihrer Arbeit ist und kein Spleen des Managements und
- den Mitarbeitern klar zu machen, dass sichere Arbeit einen wichtigen positiven Einfluss auf die Produktqualität und die Produktivität hat.
Gute und realistische Gefährdungsanalysen sind nicht nur für den bestimmungsgemäßen Betrieb, sondern auch für alle Reparatur- und Abbrucharbeiten erforderlich, denn dabei passieren häufig Unfälle.
Neben allen Regeln und Gesetzen darf man nicht vergessen, dass letztendlich keine zusätzlichen Vorschriften und Inspektoren bei der Umsetzung und Erreichung von VISION ZERO in der täglichen Routinearbeit helfen werden, denn die wichtigsten Bestandteile von VISION ZERO sind die Sicherheitskultur innerhalb der Organisation und das Sicherheitsbewusstsein in den Köpfen der Mitarbeiter. Diese beiden extrem anspruchsvollen Ziele gilt es zu erreichen.